Knitted interlining is a fabric designed to provide shape to apparel's internal fabrics. It serves to protect their outer shell against stress whilst presenting aid in areas that require stiffness including collars, cuffs, facings, chest portion pockets, and waistbands. Furthermore, interlining can save you from stretching through the wear and tear of apparel as it is available in numerous weights and thicknesses that meet each material kind's specs.
Woven Interlining Woven interlinings vary from knitted interlinings by being built out of yarns or fibers without delay, which are then woven into cotton or chemical fiber-based fabrics for weaving. Woven interlinings have long been used in garment manufacturing due to their flexibility and sturdiness, making them a fave choice in garment production.
There are four classes of woven interlinings primarily based on their construction:
(1) Hair Canvas Interlining: This form of interlining combines pure or mixed wool, cotton, goat hair, yak hair, human hair, and viscose for its weft and deform yarns to attain first-rate hardness and elasticity performance in commercial enterprise fits, jackets and overcoats. Polyester interlining can both be observed pure or mixed with chemical fiber warp and weft yarns; making polyester a fantastic cloth to apply as outerwear outerwear lining cloth.
(2) Polypropylene Interlining: Similar to Polyester interlining however cheaper and much less long lasting making Polypropylene a superb option for lower-value clothes that still want high ranges of durability along with lower-value garments that still need high ranges of durability inclusive of lower fee clothes which still require high ranges of sturdiness which include lower fee clothes want excessive ranges of durability.
(3) Polypropylene interlining: Similar to Polyester interlining but lots cheaper making polypropylene a high-quality choice while used on lower-fee clothes that still want excessive stages of durability even as ultimate price range-conscious garments want excessive degrees of durability at the same time as still wanting durability from decrease cost clothes that need durability from garments that also require sturdiness from their garments that require durability from clothes than predicted from its producer or made garments from being produced.
(4) Polypropylene interlining ought to still be used.
(5) Polypropylene interlining
Non-woven interlinings can be divided into distinct categories, fusible and non-fusible. Non-fusible interlinings are coated with powdered resin in a dot shape this is controlled with an engraved curler to decide its length, before passing the base material via it to adhere it with warmness from melting resin melted from the stated roller onto the material floor and fuse. Once sewn to shell material and fused, those interlinings must be selected cautiously on the way to not cause any harm or harm to the underlying material surface.
Fusible interlinings are designed to be long-lasting and bendy, whilst being clean to stitch. Fusibles are often utilized in formal wear to feature thickness to collars and cuffs for extra formal seems, whilst bonding them to shell fabrics facilitates stabilize them against pressure, helping prevent stretching.
Fusible interlinings should most effectively be used on the fabric of exquisite consisting of silk and georgette to attain maximum best outcomes. Their hue needs to match that of the shell fabric to lessen any visible modifications and blending problems, whilst non-fusible interlinings can be sewn into many fabrics, usually withstanding hot or bloodless water washing cycles without problem, whilst even serving as embroidery backings for clothes embellished with embroidery designs.
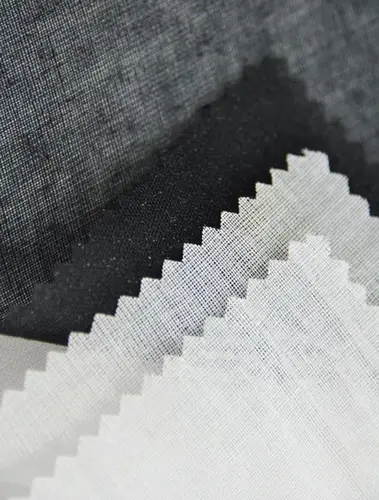
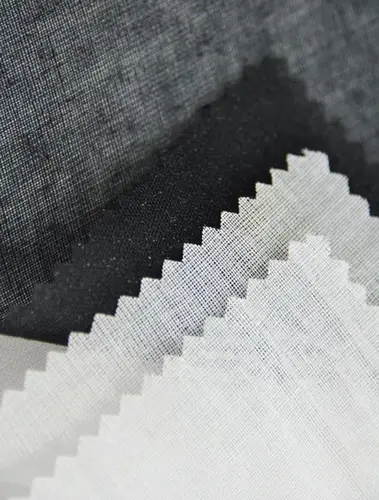