Non-woven lining is an important textile industry product. It is used in a wide range of applications, including clothing interlining and bonded lining fabrics. Its unique properties – such as softness, breathability, liquid repellency, and abrasion resistance – allow it to provide excellent support and durability to garments and linings. In addition, it can also be customised to meet specific requirements, such as high absorbency and retention for wipes, or better filtration possibilities due to the dimension and distribution of its pores.
Non woven fabrics can be made of either natural or manmade materials. Their structure is formed by parallel, cross-laid or randomly laid fibre webs that are bonded together. Non-woven fabrics can be made with a variety of raw materials, such as carded or spun-fibre webs and plastic films, as well as natural or synthetic fibres. They can also incorporate other materials, such as foam or cellulose, to enhance their performance and suitability for particular applications.
There are three main types of non woven manufacturing techniques: needle punched, wet laid and thermally bonded. In needle punch, the fibres tangle into a web while dry, and then they are bonded together using hot air. In wet laid, water is added to the fibre web while it is passing through a series of rollers. When the water evaporates, the hydrogen bonds create a strong web of fibres. Thermally bonded uses a combination of heat and pressure to fuse the fibres into a solid.
In addition, there are many other methods of producing non woven fabric. These include spray bonding, saturation and foam bonding. In spray bonding, latex is sprayed onto the fibre web on a conveyor belt. In saturation, the web is directly dipped into a latex tank and then dried in a drier. Foam bonding produces a thicker fabric by inserting a layer of foam in between the fibre webs.
The most common use of non wovens is for disposable goods, such as medical and hygiene products (diapers, surgical gowns, masks, wipes, etc). They are also used in the construction industry to control erosion and provide drainage, and in agriculture to keep silt within the soil (excess silt runoff is harmful to marine life).
Non wovens can be customisable to improve their performance or suitability to specific applications. These include adding abrasion resistance to clothing, or water resistance for liners and bags. They can also be customised to have specific colours or textures, or to increase or decrease their strength and stretch.
Besides lining, non wovens can be used in other ways, such as packaging, furniture, and automotive parts. The versatility of this type of fabric is increasing as the need for environmentally friendly materials continues to grow. Non-wovens can offer a better alternative to paper and plastic, and are easier to manufacture and recycle than traditional woven or knitted textiles. They are a cost-effective option for companies seeking to reduce their environmental impact and boost their sustainability. They are a good substitute for other forms of insulation materials, such as cardboard, and can even be used in place of fibreglass or cellulose.
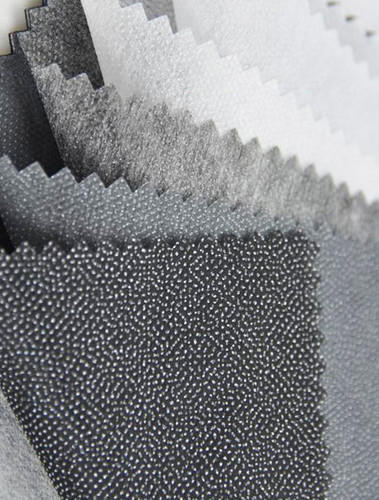
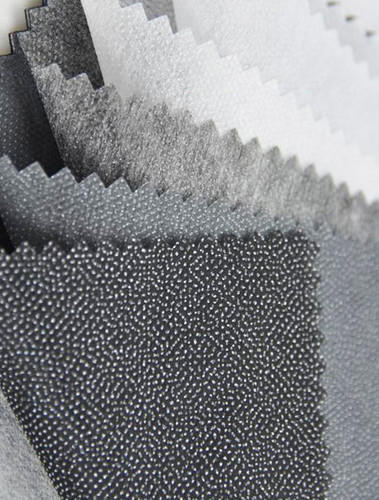