Tricot interlining is one of the most popular and versatile textile materials used for enhancing fabric structure, stability, and functionality. This material is a crucial component in the design and manufacturing of many different fabrics and garments. As sustainability and eco-consciousness continue to shape the industry, designers and manufacturers are embracing the use of this versatile fabric. Tricot interlining is a good choice for woven fabrics, as it adds softness and body to the garment while maintaining its drape and offering thermal insulation.
The rolled interlinings are the best choice for knit and woven fabrics, as they are easy to cut and sew. However, it is important to pay attention to the grainline of your fabric when working with this type of fabric. Make sure to follow the grainline, and use a serrated or straight-edge razor blade when cutting out your pieces. It is also essential to use a hot iron with steam when pressing the interlining so that it bonds properly to your fabric.
There are several types of interlinings available on the market, including woven, knitted, and non-woven. Woven interlinings are made with a warp-knit pattern that creates a dense and stable fabric. These interlinings are typically used for structured or formal garments, such as dresses and blazers. Woven interlinings are a bit trickier to work with than non-woven or knitted interlinings, as they have a selvage and will need to be hemmed before sewing.
Knitted interlinings are made of either polyester or polyamide yarns, and they are more flexible than woven fabrics. This makes them more suitable for use in clothing with stretch or recovery. Non-woven interlinings are made from wood pulp, vegetable fibers, or recycled plastic bottles. These fabrics are often less expensive than woven interlinings, but they lack the same durability and strength as woven interlinings.
Non-woven interlinings can be bonded to your fabric using a variety of methods, including spraying, printing, and heat bonding. In spray coating, the resin is sprayed onto the interlining. This can be done with the help of a spray head or by hand. The resin has a molecular size that varies from 150 to 400 microns, and the properties of the interlining vary accordingly.
The process of fusing is the most common method for attaching fusible interlining to the outer layer of your fabric. This process involves heating the assembly to a specific temperature, applying pressure, and then cooling it down again. There are several different systems for fusing, including flatbed and roller-type machinery. The most important thing to remember is that the temperature, pressure, and time must all be accurately controlled to guarantee successful results.
Fusible interlinings can be attached to the outer layers of your garments with a variety of techniques, including spraying, printing, and heat binding. When using these methods, it is essential to test your equipment before starting production, as big differences in temperature, pressure, and time can negatively impact the results.
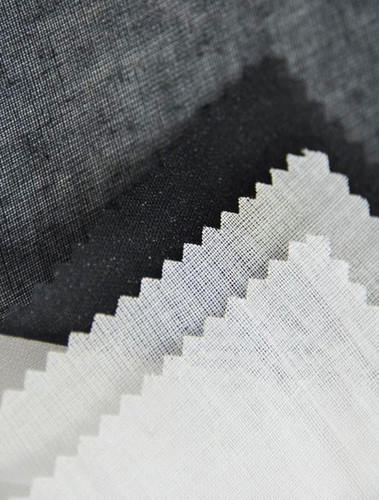
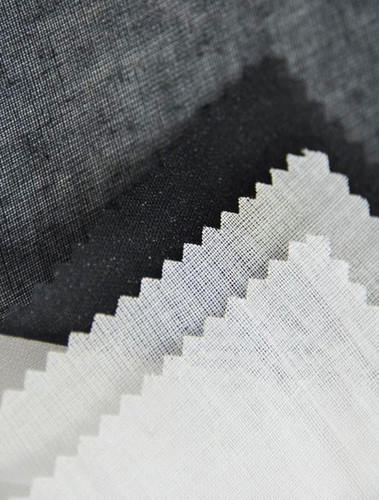